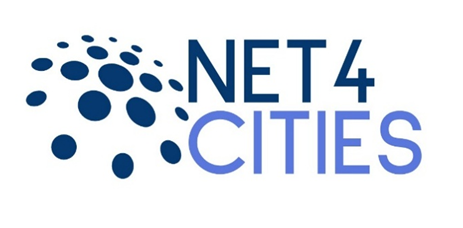
Net4Cities: Understanding Transport Emissions to Support Cities on the Path to Zero Pollution
If you’re a frequent reader of our blog, you already know that we’re deeply invested in air quality — particularly when it comes to the impact of transportation. Whether it’s engine emissions, field measurements, lab studies, or targeted campaigns, we’ve done it all. If you’re new here, you’ve arrived at an exciting time! We’re taking […]