Navigation menu
- Education
- Emissions & Air Quality
- Infrastructure & Services
- Meteorology & Climate
- News
- Physical Chemistry
- Projects
As most of our active followers know, our research group is responsible for the operation, maintenance and optimization of the Swiss Mobile Aircraft Emission Measurement System (SMARTEMIS). Typically, the system is installed in test cell 1 at SR Technics, located at Zurich Airport. In 2022 however, the SR Technics management decided to reactivate their second test cell and thus broaden their engine testing capabilities. These planned construction measures make it impossible to continue operating SMARTEMIS there until the summer of 2024. Thus, the complete system was packed and brought to Winterthur for maintenance and storage. With SR Technics’ agreement to operate our measurement system in both test cells in the future, we look forward to being able to measure the PW1100G-JM and the CFM LEAP-1B alongside legacy engines.
In cooperation with Safran Test Cells, a new exhaust sampling probe design for test cell 2 was developed. The final design is a single orifice exhaust sampling probe integrated into the blast basket cone (~25 meters downstream of the engine exit). It is much simpler than the multi-axis probe in test cell 1. A single 7 mm inner diameter probe tube will be installed concentrically with the exhaust augmenter tube. The probe location, far downstream of the engine nozzle, is chosen to keep the impact of the probe on the test cell itself as low as possible. Furthermore, the bypass air is assumed to be mixed well enough with the core flow at this location. Another important constraint is to keep the heated probe line to SMARTEMIS as short as possible to minimize particle losses.
With the temporary loss of our measuring location at Zurich Airport, alternatives had to be found to further extend the emission knowledge base in the course of the project AGEAIR II until the completion of test cell 2. Two measurement campaigns are currently in the coordination and planning phase. The focus lies in the determination of the exhaust gas composition of small unregulated jet engines with a maximum rated thrust below 26.7 kN as well as turboshaft and turboprop engines. In May, SMARTEMIS will be moved to Payerne, where the non-volatile particulate matter (nvPM) emissions of a Cessna Citation will be measured using conventional Jet A-1 and a blend with sustainable aviation fuel (SAF). A second campaign is foreseen to take place in Spain. The goal here is to be able to gather emission data of different turboprop-driven aircraft.

After a short break for data analysis, a third measurement campaign is planned in late 2023 in a European country. The core task during this campaign is to quantify the influence of different SAF blends and types on the nvPM emissions of a modern aircraft engine.
Besides the usual business, SMARTEMIS will come into play in education this spring. Two students will implement an exhaust gas probe in the existing gas turbine laboratory on the ZHAW campus in Winterthur. The modification should allow emission measurement of the SR-30 microturbine during their bachelor’s thesis. Furthermore, different blends of Jet A-1 with SAF will be investigated.
The second improvement concerns the cyclone installation. During the past measurements, the cleanliness check failed several times. In other words, when the system was sampling pure synthetic air from gas cylinders, the Particle Counter (APC), the Micro Soot Sensor (MSS), and the Scanning Mobility Particle Sizer (SMPS) measured not negligible values (APC > 2/cm3, MSS > 1ug/m3, SMPS > 100/cm3). This fact led to the conclusion that some particles are shed from the dust cup of the cyclone back into the sampling line. To prevent this, several actions have been taken but without satisfactory results. Therefore, another effort is being taken to solve this issue. To minimize the temperature difference between the cyclone and the gas flowing through it, a custom-made heating bag that covers the cyclone was ordered. Additionally, the dust cup design was changed again. It is now completely made from aluminum and consists of two parts. This makes it easier to clean the dust cup or to test different inserts if the upcoming cleanliness checks still fail.
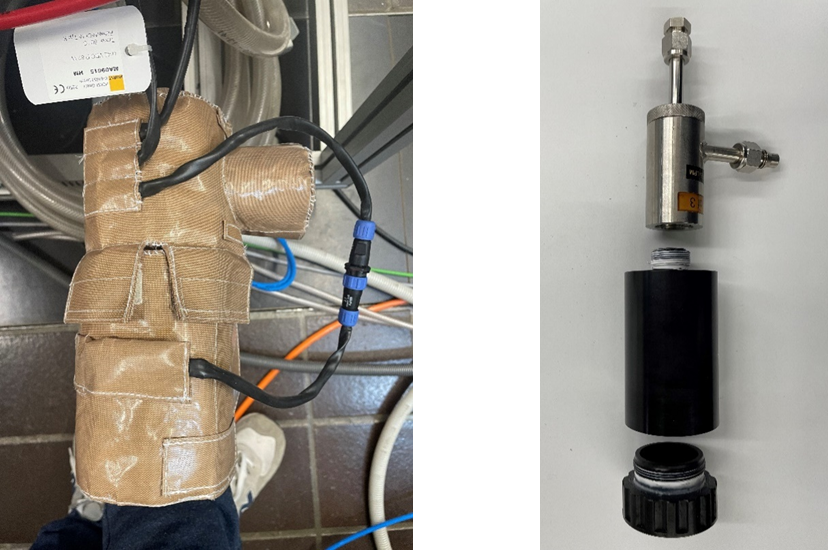
The system is completely commissioned in the laboratory in Winterthur except for the heated lines. This way, after maintenance work and modifications have been carried out, a function test can immediately ensure that all systems function as desired. Thus, the system will be fully ready for the upcoming year.
[1] L. Durdina, B. T. Brem, D. Schönenberger, F. Siegerist, J. G. Anet, and T. Rindlisbacher, “Nonvolatile Particulate Matter Emissions of a Business Jet Measured at Ground Level and Estimated for Cruising Altitudes,” Environmental science & technology, early access. doi: 10.1021/acs.est.9b02513 .