English version below
Blogautor: Daniel Schmid
Dozent, Zentrum für Produkt- und Prozessentwicklung, ZHAW, www.zhaw.ch/zpp, Schwerpunkte Industrie 4.0 und deren Einfluss auf die Produktentwicklung, Digitaler Zwilling, Sensorapplikationen
Ausgangslage
Der digitale Zwilling existiert seit geraumer Zeit. So wurde zum Beispiel in der Raumfahrt eine Zweitsonde auf der Erde belassen, um den Effekt von Steuerbefehlen vor dem Senden zur reisenden Sonde zu testen. Es war das Resultate der schieren Notwendigkeit, da die Reaktionsmöglichkeiten in den unendlichen Weiten äusserst beschränkt waren und nach wie vor sind. In der Zeit von «Internet of Things» (IoT) und der vierten industriellen Revolution «Industrie 4.0» hat der digitale Zwilling (aka «Digital Twin», «Digital Avatar») wieder an Schwung und Bedeutung gewonnen.
Zumeist wird der Zwilling als die Kombination der drei Elemente «physisches Objekt/System», «virtuelles Ebenbild» und «Schnittstelle zwischen den beiden Elementen» definiert. Unterdessen gibt es auch entsprechende Erweiterungen, um auch nichtmaterielle Güter als solchen Zwilling zu erfassen. Unter dem Begriff «Data Driven Services» entstehen digitale Zwillinge, welche über kein physisches Ebenbild verfügen und beispielsweise die Entscheidungsfindungsprozesse in Unternehmen unterstützen.
Am einfachsten kann der digitale Zwilling wohl über den Produktlebenszyklus betrachtet werden. Die drei Schritte Entwicklung, Herstellung und Betrieb werden so in die Elemente «digitaler Master», «digitaler Schatten in der Herstellung» und «digitaler Schatten im Betrieb» des Produktes aufgeschlüsselt. Der digitale Master umfasst also den eigentlichen Produktentwicklungsprozess und repräsentiert das virtuelle Ebenbild als Soll («as designed»). Fertigungstoleranzen, -schwankungen und -parameter sind die Herausforderungen der Produktion und werden im digitalen Schatten des Produkts in der Produktion abgebildet («as built»). Schliesslich wird das Produkt betrieben und somit den Umgebungseinflüssen ausgesetzt. Dies wird als digitaler Schatten des Produkts im Betrieb erfasst. Je nach Produkttyp beinhaltet dies auch Veränderungen am Produkt an und für sich (Upgrades, Firmwarewechsel, Ersatzteile, …) welche dokumentiert werden können («as maintained»).
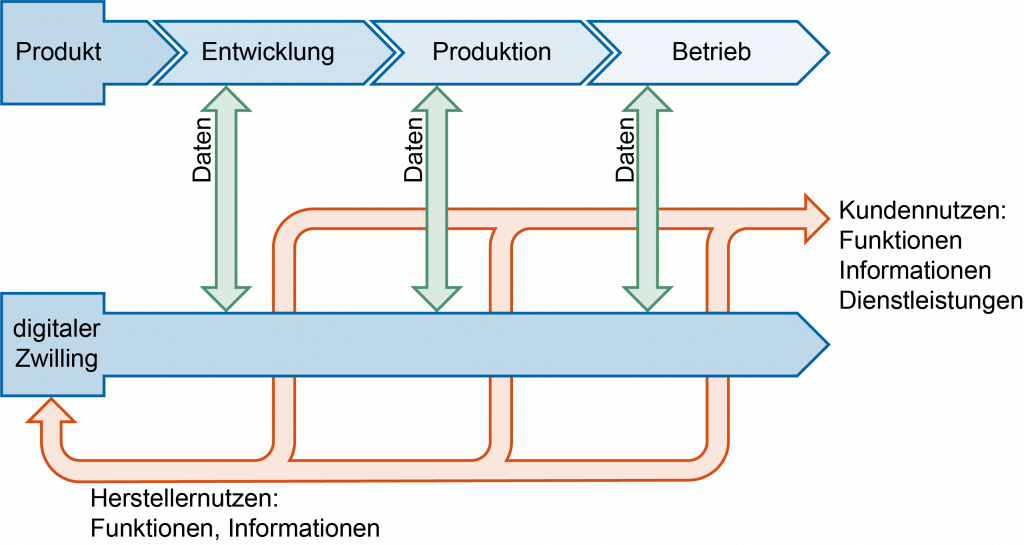
Die richtige Herangehensweise
Oft wird gefragt, wie denn der digitale Zwilling aussieht. Dies kann so direkt nicht beantwortet werden und ist eigentlich eine wenig zielführende Herangehensweise an die Thematik. Die Frage muss lauten, welchem Nutzen soll der digitale Zwilling unterworfen werden. Daraus ergibt sich schliesslich die Ausprägung. Selbstverständlich ist es auch richtig zu schauen, was heutzutage bereits möglich ist (technology push), wobei es sich am Schluss finanziell rechnen und vom Markt gewünscht und akzeptiert werden muss (market pull). Der Kundennutzen über Zusatzfunktionen und -informationen und interne Nutzen (bspw. Qualitätssicherung, Audits, …) sind also voranzustellen, um herauszufinden, ob die Investitionen lohnend sind. «Wird der Kunde mehr dafür bezahlen?», «Werde ich an Marktanteil dazugewinnen?», «Kann ich die Produktionskosten senken?» und so weiter sind die zentralen Fragen.
Wieso es nicht den digitalen Zwilling an und für sich gibt, ist auch den unterschiedlichen Produktausprägungen geschuldet. An einem Ende der Skala ist beispielsweise ein Gebäude, das in seiner Form und Anzahl einmalig ist (Smart Building). Das andere Extrem ist ein Produkt, welches in Stückzahl und Konfiguration (Variationen und Optionen) in grosser Zahl produziert wird. Weiter stehen die Produkte an unterschiedlichen Stellen in der Wertschöpfungskette. Zum Beispiel ist ein Sensor Teil einer Steuerung, Teil eines Aufzugs, Teil eines Gebäudes, Teil eines Werkgeländes und Teil einer Stadt. Ähnlich einer Matroschka ist also die Systemgrenze zu klären, um die Ausprägung des digitalen Zwillings und die Datenströme in Informationsgehalt, Auflösung und Qualität zu definieren. Ein Modell kann geradezu beliebig genau gestaltet werden. Doch nur weil die Möglichkeit besteht, ist es nicht unbedingt zweckmässig die Grenze der Physik anzustreben. Eine Steigerung des Modellkomplexitätsgrads muss auch einen ebenso grossen Zusatznutzen stiften. Um bei obigem Beispiel zu bleiben, eine «Smart City» muss nicht zwingend alle Sensorwerte aller darin enthaltenen Subsysteme kennen.
Eine Diskussion über den digitalen Zwilling eines Produkts setzt also voraus, dass der Nutzen, die Lebenszyklusphase(n), die Produktcharakteristik und die Systemgrenzen geklärt sind. Dann ergeben sich daraus die verschiedenen Disziplinen im Rahmen von Industrie 4.0, welche beigezogen und als Werkzeuge eingesetzt werden müssen.
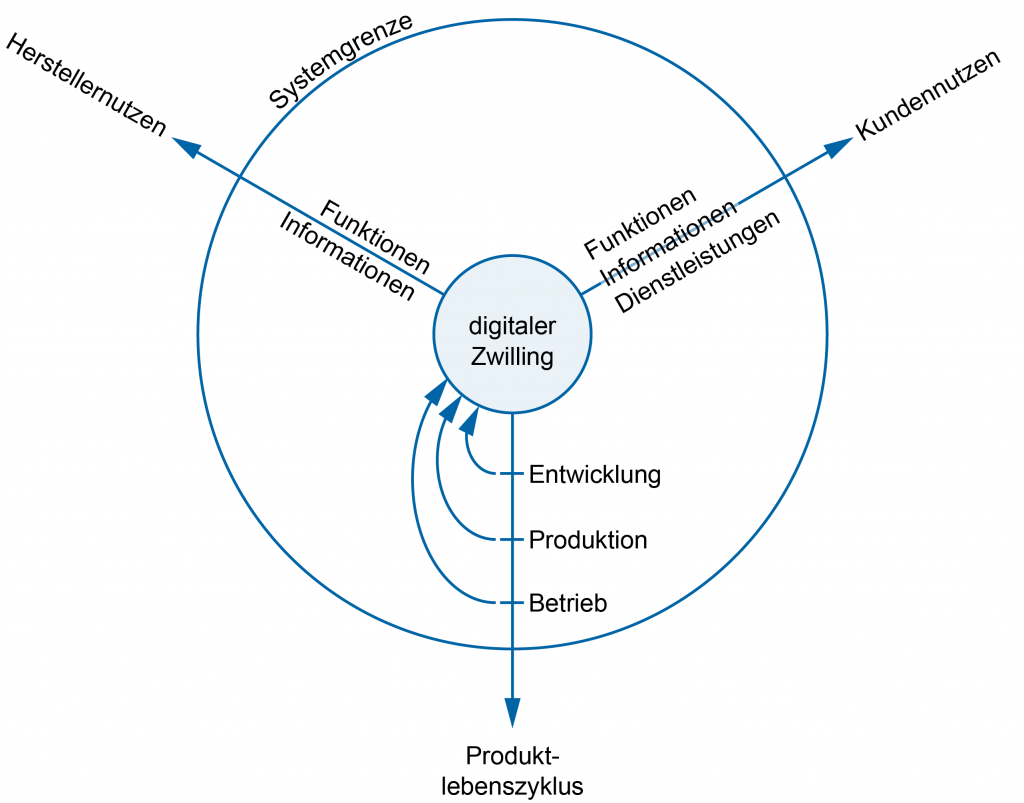
Die Produktentwicklung
Beim digitalen Zwilling ist wie bei der klassischen Produktenwicklung vorzugehen. Es ist also nicht besonders schwierig, sondern erfordert eine gewisse Disziplin, bei all den Schlagwörtern bez. IoT und Industrie 4.0 nicht die Übersicht zu verlieren. Die Anforderungen aus dem Markt und interne Bedürfnisse sind zu klären, über einen Business Case (Return on Investment) zu prüfen und in einem Pflichtenheft abzubilden. Dann durchläuft auch der Zwilling die drei Phasen des Produktlebenszyklus: Entwicklung, Produktion und Betrieb. Dies geht Hand in Hand mit dem physischen Produkt, wobei die Verknüpfungen zwischen diesem und der virtuellen Welt sich aus dem angestrebten Nutzen ergeben.
Der festgelegte Zielnutzen des digitalen Zwillings hat einen direkten Einfluss auf die Gestalt des physischen Produkts. Wenn eine Dienstleistung angestrebt wird (Data Driven Service), wie die Vorhersage des Betriebsendes eines Produkts unter Berücksichtigung des Belastungsprofils (Predictive Maintenance), müssen Daten erhoben werden. Das physische Produkt muss also befähigt werden, die richtige Datenmenge in der richtigen Qualität zu erfassen und zur Erfahrungsgewinnung zu übermitteln. Zentral ist, die Lastfälle, Verschleisserscheinungen, Betriebsdauer und so weiter zu analysieren und daraus den Kundennutzen zu generieren. Für das Anbieten einer solchen Zusatzfunktion/Dienstleistung geht der Anbieter in Vorleistung.
Auf Grund dieser Latenzzeit, auch wenn das Betriebsende eines Produkts ein Extrembeispiel darstellen mag, sind bereits heute entsprechende Entwicklungen notwendig. Bietet ein Konkurrent diese Zusatzfunktion an, ist man unweigerlich um die Grössenordnung von mehreren Jahren zurückgeworfen. Weder hat man das physische Produkt noch den dazugehörigen Zwilling entwickelt und ist somit noch nicht einmal in der Position, überhaupt Daten erfasst und analysiert zu haben.
Es ist also wichtig, die Potentiale von Industrie 4.0 für das eigene Portfolio und den eigenen Markt zu durchleuchten (Kundennutzen und eigene Bedürfnisse) und Produkt mit digitalem Zwilling dahingehend zu entwickeln – der klassische Produktentwicklungsprozess mit neuen Werkzeugen und Möglichkeiten. Mit den ersten Schritten darf nicht gezögert werden, denn schliesslich sind jegliche dazugewonnen Erfahrungen für die Zukunft entscheidend.
—————————————————————————————-
English Version:
The Digital Twin Challenge
Blog author: Daniel Schmid
Senior Lecturer, Centre for Product and Process Development, ZHAW, www.zhaw.ch/zpp,
Core area Industry 4.0 and its effect on the product development, digital twin, sensor applications
Initial Situation
The concept of the digital twin has existed for some time. In space travel, for example, a second probe would be left on Earth to test the effect of control commands before sending them to the probe traveling through space. This came of sheer necessity, since the scope for any corrective action in outer space was, and is still, extremely limited. In the era of „Internet of Things“ (IoT) and the fourth industrial revolution „Industry 4.0“, the digital twin (aka „digital avatar“) has made a comeback and is gaining in importance.
In most cases, a twin is defined as the combination of the three elements „physical object/system“, „virtual counterpart“ and „interface between the two elements“. Furthermore, we now have suitable extensions to include twins of non-material goods. Classed as „data-driven services“, digital twins with no physical counterpart are created, used for example to support company decision-making processes.
Probably the simplest way to look at a digital twin is over its product life cycle. The three steps of development, production and operation can thus be broken down into three product elements „digital master“, „digital shadow in production“ and „digital shadow in operation“. The digital master comprises the actual product development process and represents the virtual counterpart (“as designed”). Manufacturing tolerances, fluctuations and parameters are the challenges of production and are represented in the digital shadow of the product in production („as built“). Finally, the product is operated and thus exposed to environmental influences. This is defined as the digital shadow of the product in operation. Depending on the product type, this also includes changes to the product itself (upgrades, firmware changes, spare parts, etc.) which can be documented („as maintained“).
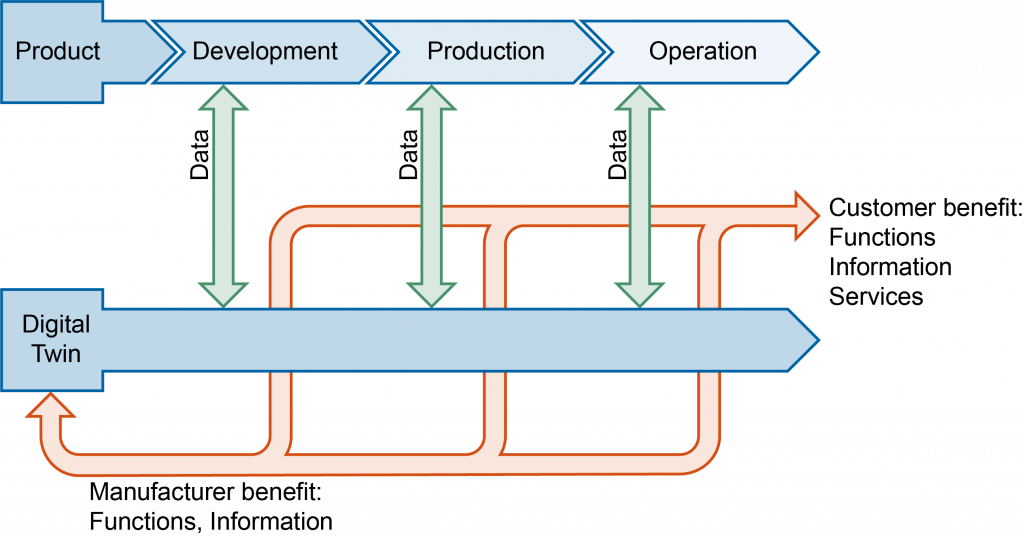
The Right Approach
People often ask what a digital twin looks like. This cannot be answered directly and is actually not a very effective way of approaching the topic. The question should be, what uses (benefit) will the digital twin be put to? After all, this is what shapes its design. Of course, it is also appropriate to verify what is currently possible today (technology push), and whether it will ultimately pay off financially and be desired and accepted by the market (market pull). The benefits to the customer from additional functions and information and the internal benefits (e.g. quality assurance, audits, etc.) must therefore be evaluated in order to determine whether the investment is worthwhile. „Will the customer pay more?“, „Will I gain market share?“, „Can I reduce production costs?“ and so on, are the central questions.
Why the digital twin as such may not exist also depends on the characteristics of different products. At one end of the scale, for example, we could have the case of a building that is one of a kind (smart building). The other extreme could be a product that is produced in large quantities and many different configurations (variations and options). Otherwise products are located at different points in the value chain. For example, a sensor is part of a controller, part of an elevator, part of a building, part of a factory site and part of a city. Like a Russian Matryoshka, the system boundary first has to be clarified in order to define the characteristics of the digital twin and the data streams in terms of information content, resolution and quality. A model can be designed with almost any degree of precision. But just because the possibility exists, it does not necessarily make sense to try to reach the boundaries of physics. An increase in the complexity of the model must also provide an equally large additional benefit. To stay with the above example, a smart city does not necessarily have to know all the sensor values of all the subsystems it contains.
Before discussing the digital twin of a product, the benefits, the life cycle phase(s), the product characteristics and the system boundaries must be clarified first. This defines which disciplines in the framework of Industry 4.0 should be harnessed and used as tools.

Product Development
To develop a digital twin, the procedure is the same as for traditional product development. It is therefore not particularly difficult but requires a certain discipline not to lose sight of the main objectives, among so many buzzwords like IoT and Industry 4.0. The market requirements and internal requirements must be clarified, checked via a business case (return on investment) and documented in a requirements specification. Then the twin goes through the same three phases of the product life cycle: Development, production and operation. This goes hand in hand with the physical product, with the links between the physical product and the virtual world resulting from the intended use.
The defined target benefit of the digital twin has a direct influence on the form of the physical product. If the goal is a service (data-driven service), such as predicting the end of a product’s service life subject to the load profile (predictive maintenance), data must be collected. The physical product must therefore be able to collect the right amount of data in the right quality and to transmit it in order to acquire experience. It is essential to analyze the load cases, wear and tear, operating time and so on, and to generate customer benefits from this. The supplier has to invest upfront to provide this type of additional function/service.
Because of this latency, even though product end-of-life may be an extreme example, these types of development are needed even today. If a competitor offers this additional function, you inevitably fall several years behind them. Neither the physical product nor its twin has been developed, so you are not even at the stage of having collected and analyzed any data at all.
It is therefore important to examine the potential of Industry 4.0 for your own portfolio and market (customer benefits and your own requirements) and to develop products with digital twins in consequence, using the classic product development process with new tools and possibilities. One should have no hesitation about taking the first steps, since any experience gained will be decisive for the future.