Blogautor: Ralf Mock
Für die Industrie, z.B. die Fertigungsindustrie und die Chemie, gehört die Suche nach Gefahren und potentiellen Störungen zum Produktionsprozess dazu. Das ist Teil des ihres etablierten operationellen Risikomanagements. Diese gilt auch nach der Transformation der Produktionssysteme in Richtung Industrie 4.0 bzw. Smart Manufacturing: Es gelten die branchenüblichen gesetzlichen Vorgaben und Standards, beispielsweise zur Arbeits- und Umweltsicherheit, um mit potentiellen oder realen Gefahren umgehen zu können. Die Erfahrung zeigt aber, dass das Risikomanagement nach ISO 31000:2018 mit den darin eingebetteten Verfahren und Prozessen des Risikoassessment (erkennen, analysieren und evaluieren von Risiken) schwieriger wird. Möchte ein Unternehmen die gewohnten Ansätze des Risikomanagements aus «alten Tagen» übernehmen, so hat es in der Praxis mit mehreren Problemen zu kämpfen:
- Die zu untersuchenden Systeme sind komplexer, da Systeme der Informationstechnik (IT) massiv an Steuerung und Regelung der Anlagen beteiligt sind.
- Mit IT Security und (klassischem) Risikoassessment kommen zwei Denkansätze zusammen, die sich nicht über alle Analyseziele und methodische Konzepte einig sind.
- Klassische Methoden des Risikoassessments kommen mit Industrie 4.0 an methodische und praktische Grenzen.
Allerdings kommt man durch das Denken in Funktionsebenen auch mit den klassischen Verfahren des Risikoassessments weiter. Zumeist lässt sich eine physische Ebene identifizieren (z.B. eine Produktionsstrecke), die über eine Kontrollebene überwacht und gesteuert wird (z.B. Leitwarte mit SCADA (Supervisory Control and Data Acquisition)). Schliesslich ist als dritte Ebene das Internet zu nennen. Eine Störung auf der physischen Ebene kann direkt Personen-, Sach- oder operationelle Schäden verursachen und ist die Domäne des klassischen Risikoassessments. Die Kontrollebene leitet über zu IT Security Risk Assessment und der Analyse von Mess- und Überwachungseinrichtungen, einschl. der Analyse potentieller Fehlern, die an der Mensch-Computer-Schnittstelle entstehen können. Die oberste Ebene sieht dann das Internet als wesentliche Infektionsquelle der Anlage durch Schadsoftware und ist die Domäne der IT Security.
Die Zusammenarbeit mit Experten und Expertinnen mit unterschiedlichem fachlichen Hintergrund gestaltet sich mitunter unerwartet schwierig. Diese Schwierigkeit kann dadurch entstehen, dass für die IT Security Daten und Informationen als Assets des Unternehmens das primär zu schützende Gut sind (und die Bedrohung der Assets von aussen kommt). Für das klassische Risikomanagement sind jedoch Personen und die Umwelt das zu schützende Gut, das hauptsächlich durch unternehmensinterne Gefahren, z.B. durch die Freisetzung gefährlicher Stoffe, bedroht ist. Mit der Industrie 4.0 kommen somit zwei Bereiche zusammen, die in früheren Tagen nebeneinander ihre Aufgaben erfüllen konnten. Das Management eines Unternehmens sollte sich dieser unterschiedlichen Denkschulen bewusst sein, um die Prozesse eines modernen Risikomanagements effizient gestalten zu können.
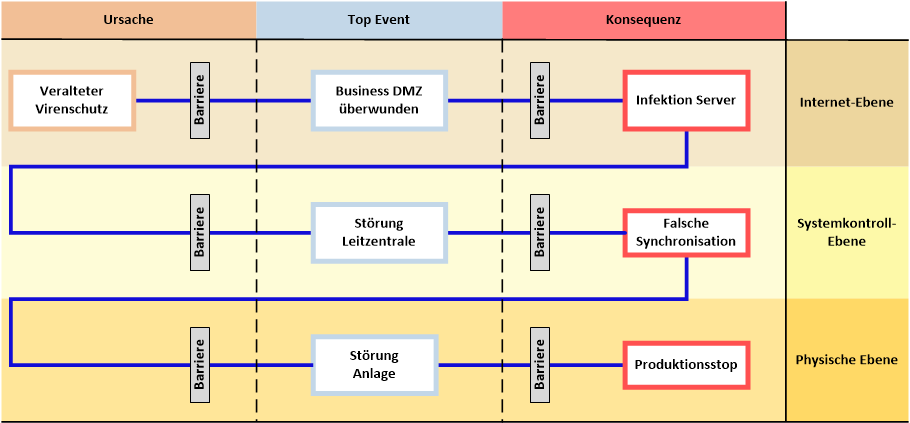
Die Verknüpfung über die drei Ebenen kann auch die bekannte Methoden des Risikoassessments nutzen: Das Bow Tie Diagram und die Failure Mode and Effects Analysis (FMEA) sind weitverbreitete und praxisnahe Werkzeuge des Risikomanagements in einem Unternehmen. Beide Methoden helfen dabei, die Ursachen eines unerwünschten Ereignisses (z.B. ein Serverausfall) und die daraus resultierenden Konsequenzen zu beschreiben. Sie berücksichtigen auch vorhandene Gegenmassnahmen. Die FMEA versucht darüber hinaus, Häufigkeit und Ausmass des Ereignisses abzuschätzen, und damit eine Risikozahl zu generieren. Mit dem Ansatz der drei Funktionsebenen lässt sich der klassische Ansatz neu strukturieren und im Sinne des Risikomanagements des Gesamtsystems in der Industrie 4.0 vervollständigen. Beispielsweise kann ein veralteter Virenschutz als Konsequenz die Infektion eines Servers auf der Kontrollebene bedeuten und ist hier die Ursache für die Übermittlung eines falschen Steuerwertes an die leitzentrale. Dies ist dann wiederum die Ursache für einen falsch synchronisierten Produktionsprozess, was einen Produktionsstopp zur Folge haben könnte. Eine etwas erweiterter Ansatz ist, dass man die unabhängig voneinander erstellten Analysen auf den Funktionsebenen nach Ursache-Wirkungs-Ketten über alle Ebenen hin untersucht und die Ergebnisse miteinander verbindet.
Im Fazit macht Industrie 4.0 die Risikomanagementprozesse nach ISO 31000:2018 nicht einfacher. Sie verlangt die (noch) engere Zusammenarbeit von (noch mehr) Personen aus den verschiedensten Fachgebieten, die im Unternehmen fachlich und organisatorisch (noch) enger zu koordinieren sind. Dies kann nur über ein übergreifendes und gemeinsames Verständnis zu Methoden und Zielen des Risikomanagements erfolgen. Der CAS Industrie 4.0 der ZHAW liefert hierzu einen Beitrag.